Wat niet past, wordt passend voorbereid.
Op hoop van zegen? – echt niet! Tijdens de overgang naar de TI-50 hebben de verantwoordelijken niets aan het toeval overgelaten. De officiële start van de productie van de nieuwe behuizing TI-50 in januari 2021 was een belangrijke mijlpaal. Dat deze lancering zo soepel verliep, is geen toeval. De voorbereidingen waren zowel intensief als inspannend, maar ze waren het waard, zoals het resultaat laat zien.
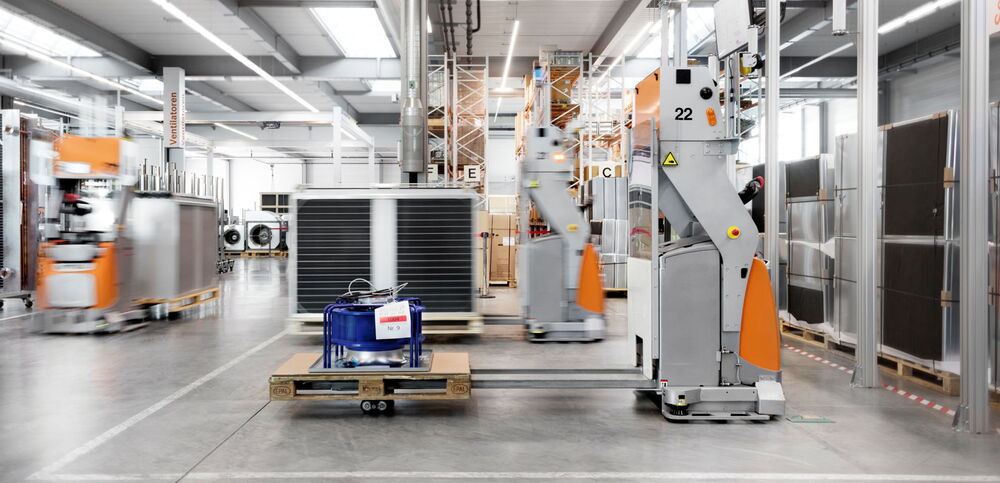
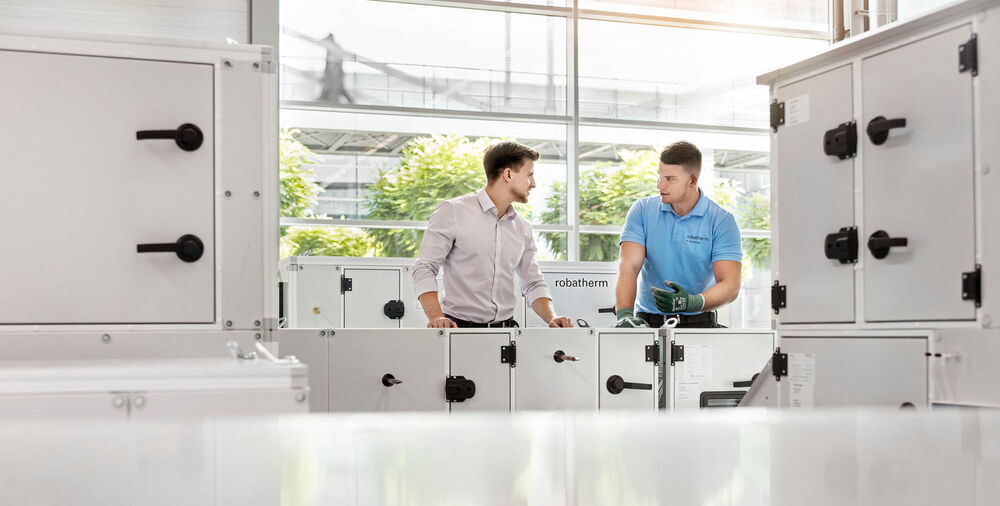
De productie- en ontwikkelingsingenieurs bij robatherm spreken van „simultaneous engineering“ als ze het over de ontwikkeling van TI-50 hebben. In feite betekent dit dat afzonderlijke ontwikkelingsstappen, die traditioneel na elkaar plaatsvonden, elkaar met deze methode in de tijd overlappen. In het geval van de ontwikkeling van TI-50 zou dit waarschijnlijk in het verleden zijn gedaan door een concept te ontwikkelen van hoe de behuizing er in de toekomst uit zal zien. Daarna zou de productie zijn begonnen met het integreren van dit nieuwe behuizingsconcept in hun productieprocessen.
Eventueel zou dit in een laat stadium van de ontwikkeling weer hebben geleid tot fundamentele wijzigingen aan de behuizing. Een met name tijdrovend proces. Het projectteam van robatherm heeft door middel van simultaneous engineering bewezen dat dit ook anders kan.
Haalbaar? Haalbaar!
De belangrijkste basis is vroegtijdige communicatie en afstemming tussen ontwikkeling en productie. Het ging er immers ook om niet alleen de productkwaliteit maar ook de processen in de productie verder te verbeteren en zo de efficiëntie bij de vervaardiging te verhogen. Al in de vroege fase van het project werden prototypes en haalbaarheidsstudies gemaakt. Zo kon al in een vroeg stadium worden gecontroleerd of ideeën realiseerbaar waren en in de praktijk ook echt zouden werken.
11.800 thermopanelen tot aan het startsignaal
Al vanaf mei 2019 werden TI-50 luchtbehandelingskasten met toenemende complexiteit geproduceerd in een nulserie. Elke geproduceerde samenstelling en luchtbehandelingskast werd nauwlettend gevolgd en gecontroleerd door een team van ontwikkeling en productie. De bevindingen uit deze voorserieproductie vloeiden direct terug in de ontwikkeling en de structuur van de processen. Tot aan de start van de serieproductie in januari 2021 werden er o.a. 11.800 thermopanelen en 2.200 deuren van de nieuwe behuizing TI-50 geproduceerd.
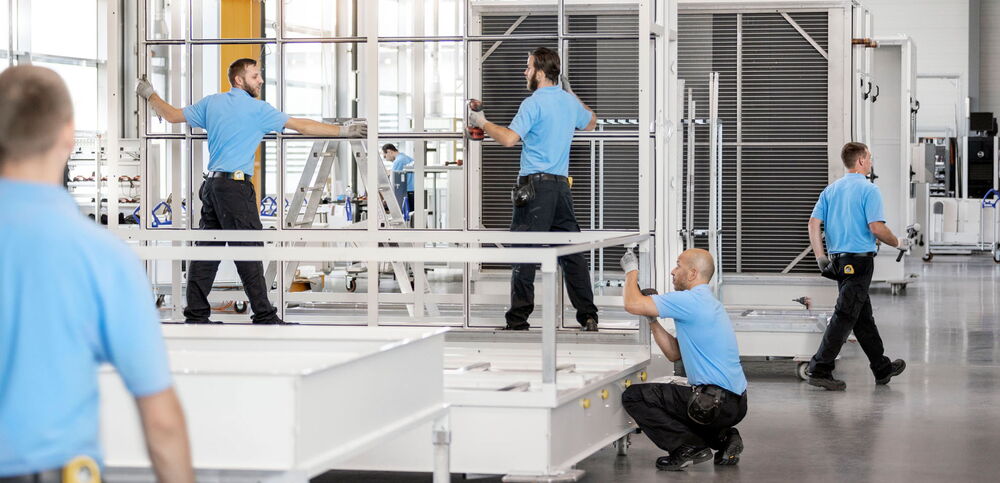
Betrokkenen worden participanten
Tijdens elke fase werd feedback gevraagd van allerlei teams uit de productie en assemblage. Deze inzichten werden direct verwerkt in de ontwikkeling. Dit verbeterde niet alleen de kwaliteit van de nieuwe ontwikkeling, maar verhoogde ook de identificatie van de medewerksters en medewerkers met de nieuwe behuizing en hun acceptatie van veranderingen in toekomstige werkprocessen. Het productiepersoneel volgde al tijdens de testfase een theoretische en praktische training. Om dit mogelijk te maken, ondanks de reguliere productieactiviteiten, werd de training georganiseerd op basis van roulatie.
Wijzigingen in hardware en software
De introductie van TI-50 vereiste uitgebreide aanpassingen in de software en IT-infrastructuur, in de productieprocessen, in het machinepark, in de vormgeving van de werkplek of zelfs in het beschikbaar stellen van materialen. Alleen al voor de inkoopafdeling betekende de overgang naar TI-50 dat er bijna 100 nieuwe koopdelen aan het portfolio werden toegevoegd. De veranderingen in de productie werden duidelijk in een volautomatisch zaagcentrum. Dit werd aangeschaft en geïntegreerd in het machinepark om de afzonderlijke profielvarianten voor de productie van thermopanelen beter te kunnen reproduceren.
De uitdaging: synchrone productie van twee soorten behuizing
De parallelle productie van twee behuizingsseries, zowel de vorige serie als de nieuwe TI-50, vormde een speciale uitdaging voor de productie. Voor de start van de serieproductie waren er al proeflijnen in gebruik genomen en waren de werkplekken voorbereid op de overgang naar de TI-50. Terwijl de testkasten steeds complexer werden en ook hun aandeel in de productiecapaciteit bleef toenemen, moest er tegelijkertijd voor worden gezorgd dat de processen voor de productie van de vorige behuizingsserie niet in het gedrang kwamen.
Een rustige kerstvakantie? Dacht het niet.
De definitieve omschakeling naar TI-50 vond plaats tijdens de kerstvakantie, zodat het startsein voor TI-50 vanaf januari 2021 gegeven kon worden. Tijdens de zogenaamde vrije tijd bereidde een team o.a. de assemblagelijnen en hun werkplekken voor. In de productielocaties in Jettingen-Scheppach en Burgau werden ongeveer 1.000 opslaglocaties omgebouwd en ca. 1.750 bakken, zogenaamde eurocontainers (kleinere industriële stapelcontainers), vervangen.
Tijd voor een nog langere testfase
Dankzij simultaneous engineering konden volgende ontwikkelingsstappen al worden afgetrapt zodra er voldoende informatie was verzameld in de voorgaande ontwikkelingsstap. Met de volgende etappe wordt dus niet pas begonnen zodra de eerste stap volledig is afgerond. Dit leidde tot een hoge communicatie-inspanning maar ook tot een aanzienlijk snellere ontwikkelingstijd. Een tijdsbesparing die uitgebreid kon worden gebruikt voor praktijktests. Dankzij deze intensieve tests was de TI-50 op het moment van de officiële lancering niet alleen klaar voor de markt, maar had zich ook al in de praktijk bewezen.
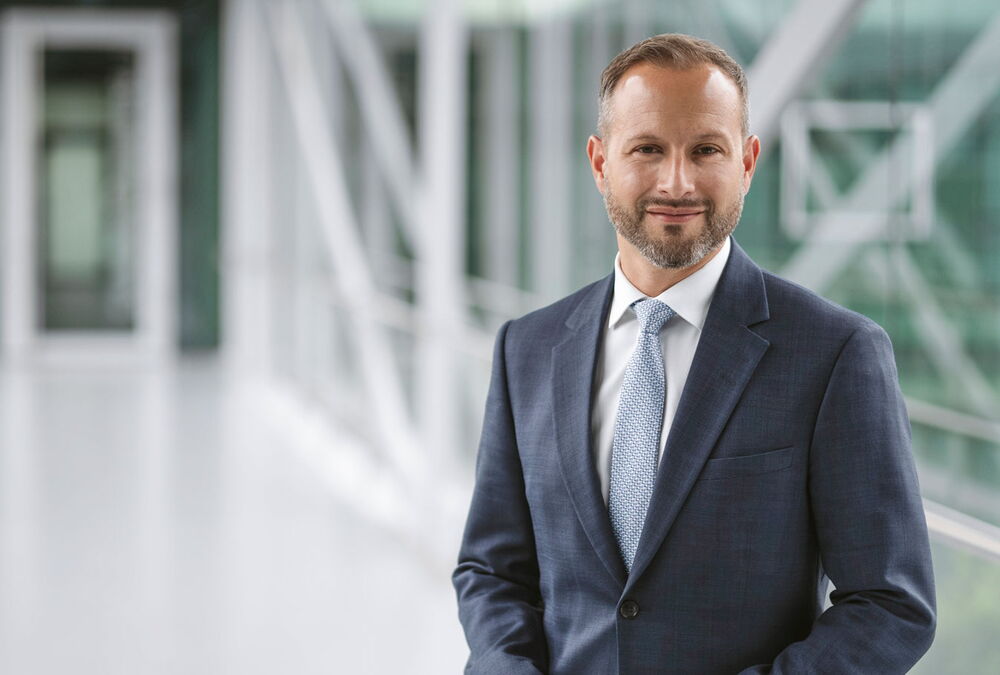
„De start van de productie verliep uitstekend dankzij al het werk van het hele projectteam.“
Andreas Lamprecht
Hij is o.a. verantwoordelijk voor de productielocaties in Jettingen-Scheppach en Burgau.